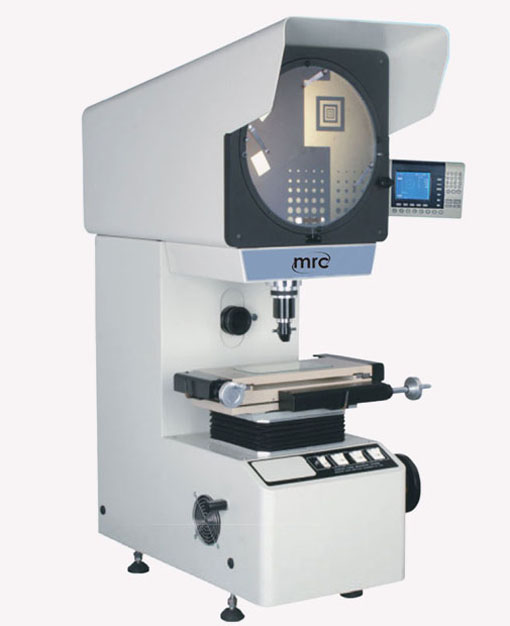
We Provide A Comprehensive Range Of Quality Assurance
Quality Assurance (QA) is proactive and process-oriented, focusing on setting up procedures to ensure quality standards are met at every stage of production.
Metal Hive Network QA begins with establishing quality standards and specifications that define acceptable levels for factors such as size, material, functionality, and appearance. Standards may include ISO, ANSI, or ASTM specifications, industry-specific standards, or internal company standards.
Developing Quality Plans QA teams create a quality plan that outlines how the quality objectives will be met, detailing each process step, inspection point, and standard to follow. Plans also include risk management strategies to identify and mitigate potential issues.
Technologies like vision systems and AI-driven inspection allow for precise
1. Quality Assurance (QA): is proactive and process-oriented, focusing on setting up procedures to ensure quality standards are met at every stage of production.
2. Quality Control (QC): is reactive and product-oriented, involving inspections and testing of the product to detect defects after production.
1. Setting Quality Objectives: Clear quality objectives are established based on customer needs, regulatory requirements, and internal goals. Objectives might include minimizing defects, reducing variation, or improving reliability.
2. Developing Quality Plans: QA teams create a quality plan that outlines how the quality objectives will be met, detailing each process step, inspection point, and standard to follow. Plans also include risk management strategies to identify and mitigate potential issues.
1. Statistical Process Control (SPC): SPC uses statistical methods to monitor and control production processes, tracking data points like variation, defect rates, and cycle times to detect any deviations from standards. Control charts, for instance, help detect trends that could lead to defects.
2. In-Process Inspections: QA includes inspections at different production stages to identify issues before products progress. This can be done through visual checks, automated sensors, or sampling methods to verify that standards are maintained throughout production.
3. Non-Destructive Testing (NDT): NDT methods, such as X-ray, ultrasound, and dye penetrant testing, are used to assess material quality and structural integrity without damaging the product. This ensures quality without sacrificing components to testing.
1. Product Testing: QA involves testing products under controlled conditions to validate their performance, durability, and safety. Testing types include load testing, environmental testing (heat, cold, moisture), and lifespan testing, ensuring the product performs as expected.
2. Prototype Testing and Validation: Prototypes are tested early in the design phase to identify design flaws and make necessary adjustments before full-scale production. This reduces costly changes later in production.